VEGGIE-PLASTIC CONTINUES TO PROTECT SHIPS AND BOATS AFTER TWO DECADES!
- Eric_Byctt
- Jan 15, 2020
- 3 min read
“Setting aside the zero VOCs for a moment, it’s all in the adhesion and retained flexibility,” says Eric Boycott, CEO of Richmond, British Columbia, coating protection firm, Eurasia Building Technologies Corporation.
“For all practical purposes, this vegetable oil-based coating has a grip that is off the charts when it comes to the standard adhesion tests. That is so important on vessels that are not only subject to extremely harsh climate conditions but also the structural movements induced by heavy seas and machinery.
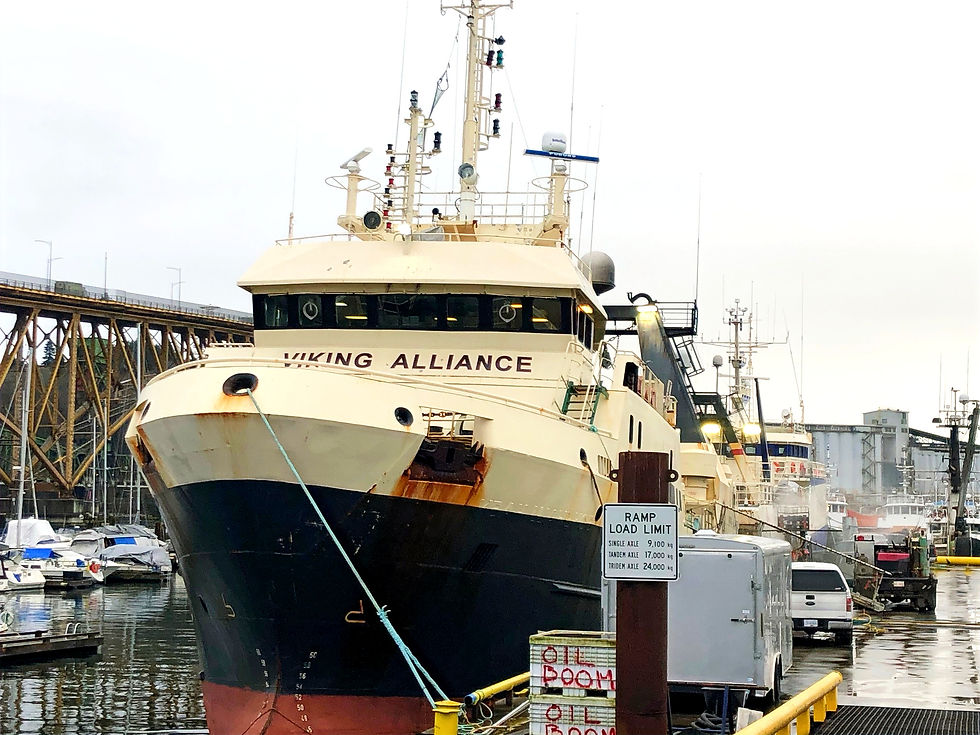
“Many conventional epoxies and polyaspartics, especially on large vessels, last only a matter of a few weeks before they microcrack and start letting in saltwater, especially along weld seams.”
Made from castor oil and gypsum that was first pioneered nearly 30 years ago in nearby North Vancouver, 20-year plus lab brine tests and submersion in dock seawater, have shown no measurable deterioration whatsoever, other than a harmless surface coating of algae.
Original epoxy coating is cracking and letting in seawater into the steel deck causing rust
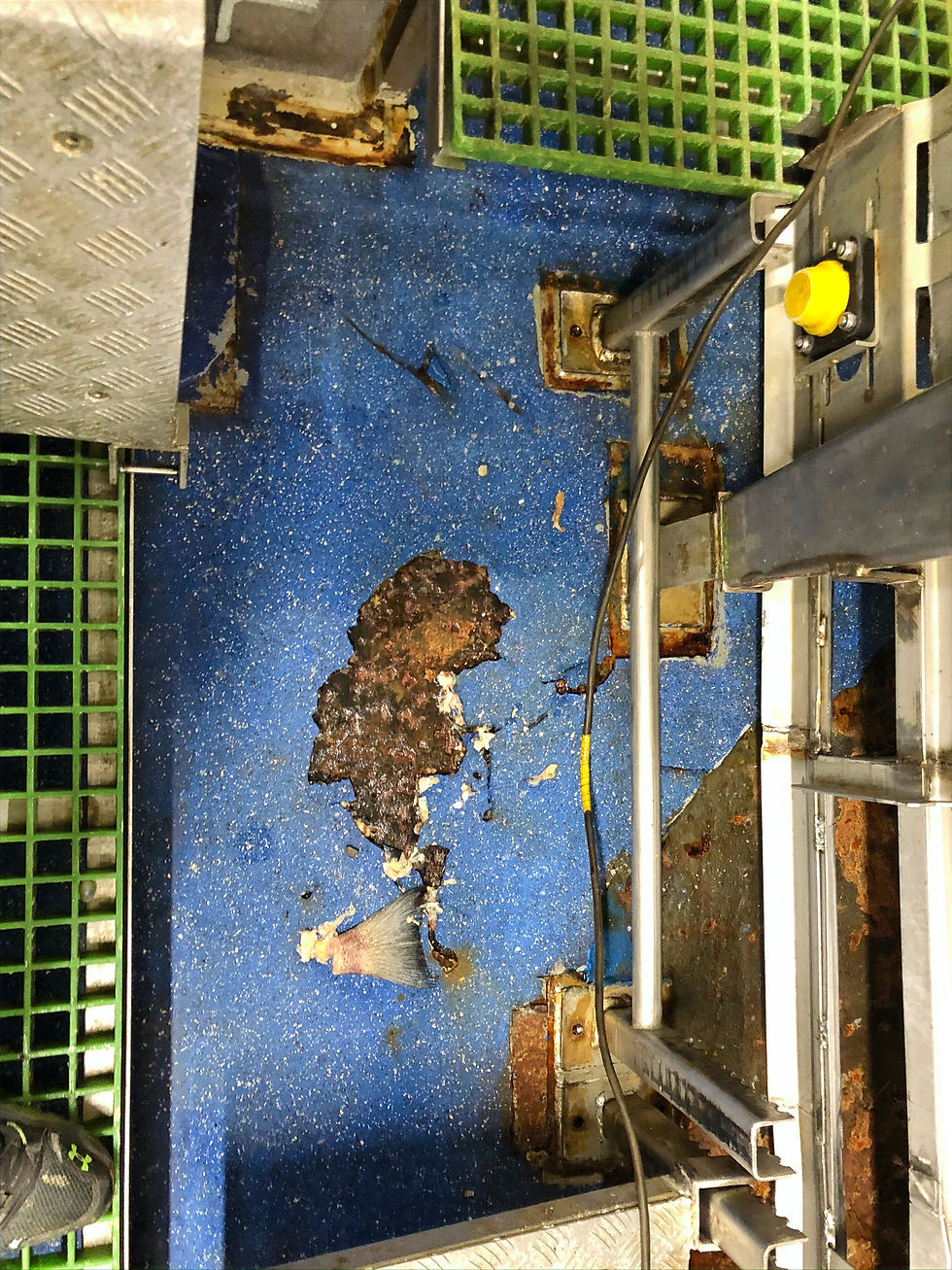
Now called Ecodur, the non-toxic coating was first applied on C-Class ferries in BC Ferries fleet. It has been used on small vessels as well as a giant fracking ship and today, Boycott’s team have just finished up internal coating of repairs on two fish factory ships, the trawler Viking Alliance, which was built in 1996 with a carrying capacity is 401 t DWT and the smaller trawler Northern Alliance at 229 t DWT carrying capacity.
Both trawlers had problems common to hardworking steel vessels - rust. Heavy machinery bedded on the decking with reinforced footings had been protected with an epoxy that had failed and allowed saltwater to get in and corrode. Remedial work had entailed chiseling, scaling, wire brushing and cleaning with solvent down to metal back to where the substrate showed its original integrity.
Castagra Ecodur coating is sealed over the steel deck

The work was carried out by Olaf Haeussler whose specialty is exotic materials and processes. “In this case, there’s nothing exotic about a fish factory with its cleaning and flash freezing, but the process is a tough one on the ship’s infrastructure, especially the pressure washing with high hydraulic pressures that will allow water to seek out any weaknesses.
“To anyone familiar with steel boats and ships that work the sea, the sea is always winning, albeit slowly. The best remedial work can do is stave off the timing of the next fix. In this case, we get to push out time longer by using a proven and more robust coating which, in this case, is a naturally derived one that has phenomenal adhesion and resistance to the rigors of fish factory regimes.”
The coating, Ecodur, was first invented in the early 1990s by Peter Roosen, then a resident of North Vancouver. Today, the coating is in thousands of oil and production water tanks, drinking water tanks, and innumerable floors and flat roofs.
It is ANSI/NSF-61 certified for contact with human drinking water and is Class A rated as a flame retardant. With no BPA it also has the unique ability to re-bond to original coatings making future remedial work far more effective.
“You could call it an 'editable' coating. You can fix problems beneath it any time, even in the distant future with 100% confidence that the repair will be seamless with the original Ecodur around it and perfect in terms of protection,” concluded Haeussler.
Comments